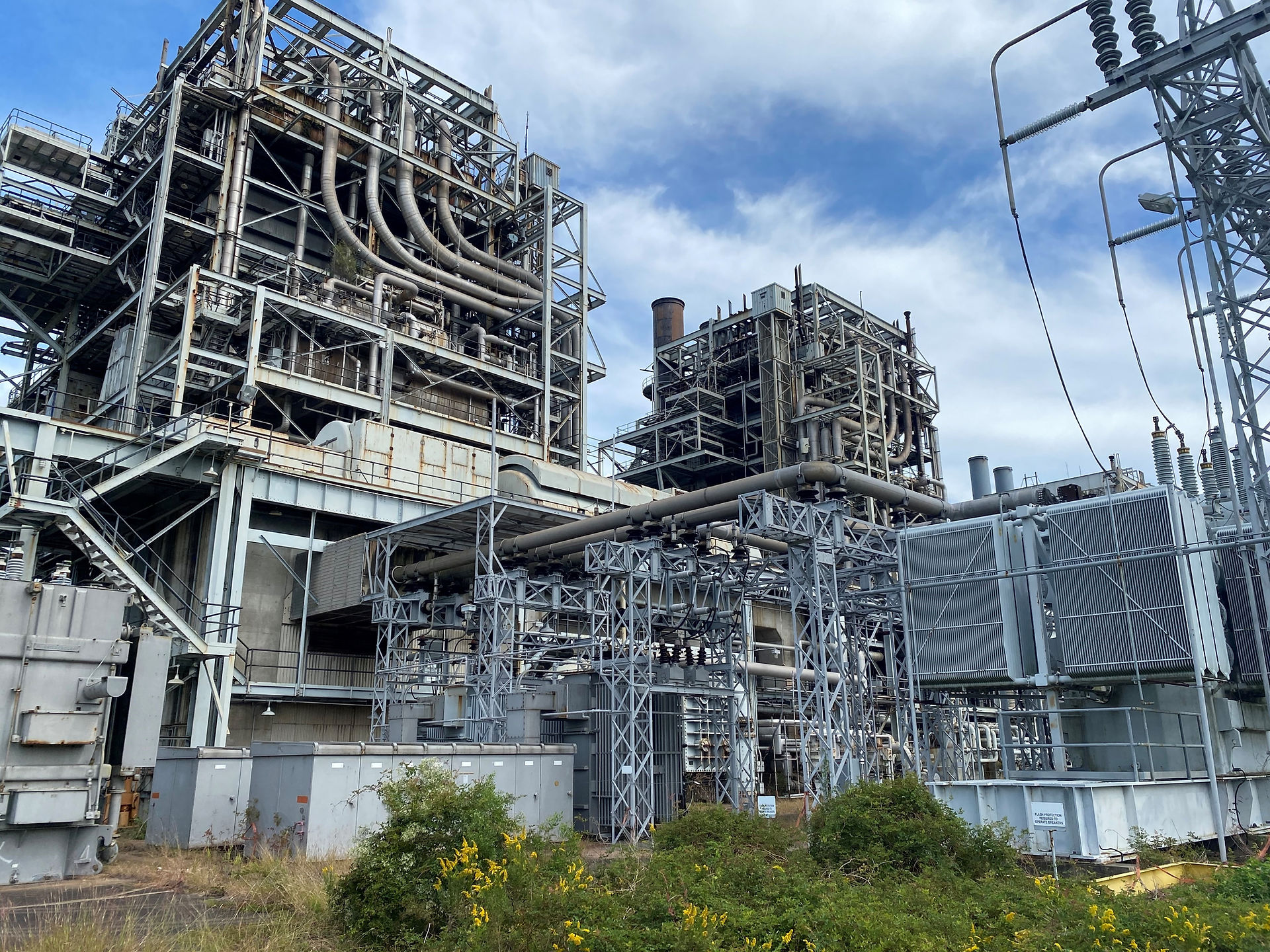
Safety is
Our Strength
With over 35 years of industry-leading experience, AMS has established an enviable track record of excellence in safe practices through our first-class safety programs and management philosophy, centered around our customers and employees. Our technical expertise, experience, and commitment are also focused on ensuring that a “zero accident” performance goal is accomplished and sustained for the entirety of every project we tackle. Because at AMS safety is more than our philosophy, it’s our way of doing business.





Established protocols for protection, safety, and control are enforced at each job site.
All AMS Group field personnel receive OSHA training tailored to meet or exceed site-specific requirements, such as OSHA 10 and OSHA Hazardous Waste Operations and Emergency Response (HAZWOPER) certification.
​
Being environmentally and safety conscious, AMS Group has developed proprietary specialty contractor decommissioning techniques. This includes eliminating fire hazards and avoiding lead exposure during our processing of all non-hazardous oil-filled equipment.
​
Whether in our own facilities or client’s site, we strive for zero incidents. Our focus on safety and training reflects this commitment. It is essential to remain proactive in the area of safety, which is reflected in the unwavering quality of our work provided to our clients.

AMS’ top priority is a safe working environment for our crews and clients.
Our Goal: Zero incidents with a Safety Programs That Deliver Results
Safety Is a choice
we make
and a choice
we stand by.
As a part of our HS&E programming, we maintain a safe and healthy work environment through diligent application of standard health and safety procedures that comply with the Code of Federal Regulations per 29 CFR 1910 Federal regulations, environmental awareness, and on-the-job safety are integral parts of our safety-training efforts. We conduct in-house ongoing safety training, division safety meetings, project-specific job-safety analysis, and daily job walks.
-
Who is accountable for?AMS: Leading the job. AMS: Managing the contractors.
-
Have the job hazards been clearly identified?JSA exists or to be developed LOTO PPE available / limitations understood Gravity / Lighting / Lifting Asbestos / Lead
-
Has a written set of expectations (check list) been developed?Step-by-step plan Skills needed Training required Tools required Applicable policies, procedures, permits
-
How will the plan be communicated to the workers and operations?Field worker review of plan Pre-job briefing (JSA) Communications with control room start/stop of job Between shifts
-
What will the people involved do if there is a problem with the plan?Stop when unsure and notify the leader Rescue contingency Human performance issues (time stress, job focus, routine, 3-way communications)
-
How will we monitor progress and define success for the job?Predetermined expected results Metrics Status updates / meetings Management oversight (on shift) Worker feedback included As left housekeeping Document lessons learned and communicate to the fleet
-
Who is accountable for?Developing the quality plan Implementing the quality plan Reviewing the quality plan data Reviewing a vendor’s/contractor’s quality plan
-
Has a detailed quality plan/expectations check list been written?Critical disassembly / reassembly steps identified Critical measurements identified Inspection hold points identified Critical measurement independent verifications identified All data written down for follow up review Original codes / standards OEM documentation referenced Required tools / test equipment Previous lessons learned Special training / certification requirements
-
How will the plan expectations be communicated?Craftsman review Pre-job briefing Shift turn over logs Schedule inputs If the plan changes With the control room
-
How will the plan be implemented?Over various shifts Foreign Materials Exclusion (FME) protection Management oversight / periodic review Tools / equipment calibrated and available Critical part receipt inspections Critical vendor visits
-
What will happen if a problem is identified in job quality?High risk contingency plans developed Stop when unsure and notify the leader
-
How will we monitor performance and measure success?Predetermined expected results identified Status updates / meetings Management oversight and visual observation (in field) Data review Start up readiness checks and tests (i.e., NDE) Testing / monitoring of equipment during equipment start up Worker feedback included Job documentation complete and in job history Document lessons learned and communicate to the fleet
-
Who is accountable for?Identifying the risk Ensuring the right resources are available (physical, data, personnel, etc.) Ensuring the right procedure, checklist, training is in place
-
How do we identify that this is a risk situation? (Safety, Protecting the asset, Quality, Environmental, Financial, Community, Regulatory)Can you afford to be wrong? Could we experience significant safety issues? Can the company reputation be affected? Could failure result in significant impact to operations?
-
Have the expectations regarding the risk been managed?Has management put their eyes on the issue? Is there a written plan to address the various risks? What are the options? (Timeline, recommendations) Establish the requirements, design limits What are our options and the consequences of each? How long do we have to make the decision? What level of authority is involved in making the decision?
-
Have risk considerations been included in the plan?History with this job / risk Notifications – appropriate escalation (transparency) Who has the capability to do the job? What is the cost? Have we included post-test requirements? What tools do we have and what do we need?
-
How will the plan expectations be communicated?Field worker review of plan Communications with control room start/stop of job Stop when unsure and notify the leader
-
How will we monitor success regarding risk?Effectiveness review Document lessons learned and communicate to the fleet Review extent of condition of risk Determine if the risk is managed properly
COMMITMENT TO SAFETY
AMS Group has an extensive training and safety education program that encompasses all aspects of our industry and fieldwork. We have seasoned safety officers leading our program in the field and at our Houston facility. This includes 30-hour OSHA Standards, Corporate Safety Manual, and First Aid/CPR training for our front-line supervisors.
​
Our safety programs are wide-ranging and flexible, with the ability to incorporate industry- and site-specific requirements for behavior-based safety, lockout/Tagout, and subcontractor safety. On-site work starts each day with our weekly planned JSAs.
Our Job safety analysis (JSA) identifies, analyzes, and eliminates potential hazards and risks associated with specific job tasks and equipment to be in use. It ensures that all proper safety measures and protective equipment requirements are in place.
Our program incorporates protective measures for all known hazards and we have identified some as follows:
-
Fall hazard: A comprehensive approach including formalized fall arrest plans for every project.
-
Line-of-sight: Supervision requirements to ensure that work is done within sight of a supervisor or foreman, and every incident investigation we conduct addresses this requirement.
-
Safety incentive plan: Provides significant financial incentives to workers, lead foremen, supervisors, and site safety officers who maintain high performance in the areas of compliance, safe behaviors, and injury prevention.
In any environment, challenging or complex, we take on projects with a commitment to safety that is unparalleled. Whether in our own facilities or at a customer’s site, our goal is always zero accidents or injuries, and our focus on safety and metrics reflects this.
ENVIRONMENTAL COMPLIANCE
The operations of AMS Group comply with all federal and state environmental laws and
regulations as specified below.
​
U.S. Environmental Protection Agency (EPA)
PCB Commercial Storage and Decontamination Permit.
Texas Department of State Health Services (Texas DSHS)
Worksite Wellness
Texas Commission on Environmental Quality (TCEQ)
• Used Oil Handler Permit ID # TXR000081501
Petroleum Storage Tanks (PSTs): our facility maintains PSTs that hold fewer than 1100 Gal. ea.
Air Permits – our Houston, TX facility does not process material for combustion and therefore
Air permitting is not required.
​
Storm Water Permit: The City of Houston requires an annually renewable Storm Water Quality
permit for any new development of an undeveloped parcel of land five acres or larger, or
significant redevelopment of changes of one acre or more to the impervious surface.
AMS corporate facility is on a half-acre of land, eliminating this permitting requirement.
For additional information and compliance with the MS4 permit, see the City Ord. No. 01-800
(Code of Ordinance Chapter 47 Article 12) adopted in 2001